Lian Rou Machinery is dedicated to creating personalised mattress customisation solutions to help customers seize the first opportunity in the custom mattress market.
Ordinary mattresses:
Sleeping on your back - if the mattress is too soft, your torso will sink in; if the mattress is too hard, parts of your torso will not be supported.
Sleeping on your side - if the mattress is too soft, your torso will sink in; if the mattress is too hard, parts of your torso will not be supported.
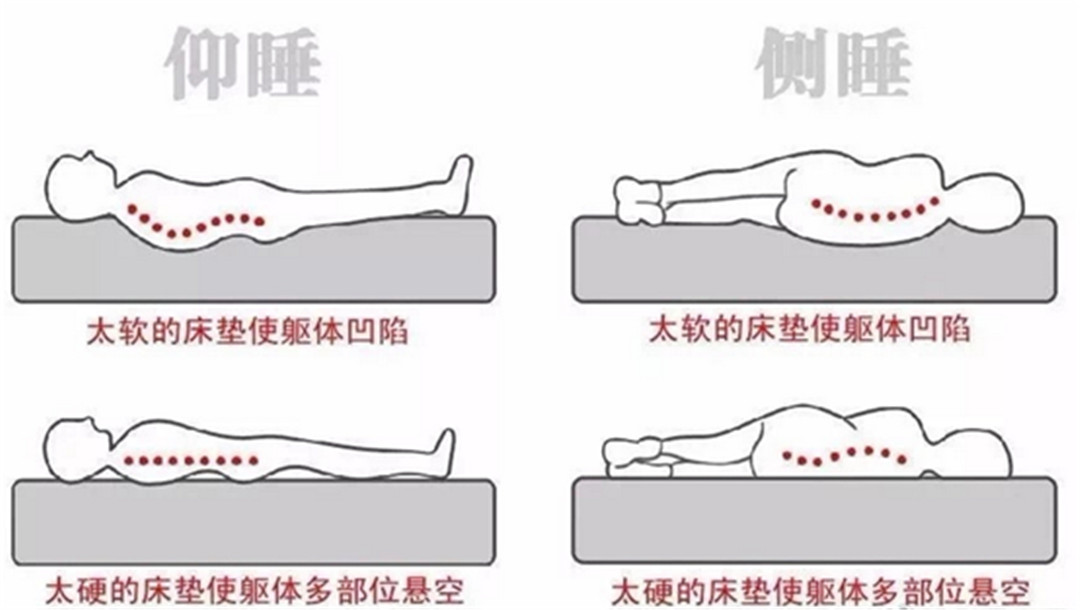
Custom mattresses:
Ergonomic design
Zoned support for spinal health
Conforms to the curves of the body, evenly distributing body weight to reduce pressure on the spine, muscles, blood vessels and nervous system, helping to maintain spinal health during sleep
Lian Rou Machinery's comprehensive and complete mattress personalisation solutions are highlighted and attractive, solving healthy sleep problems for users.
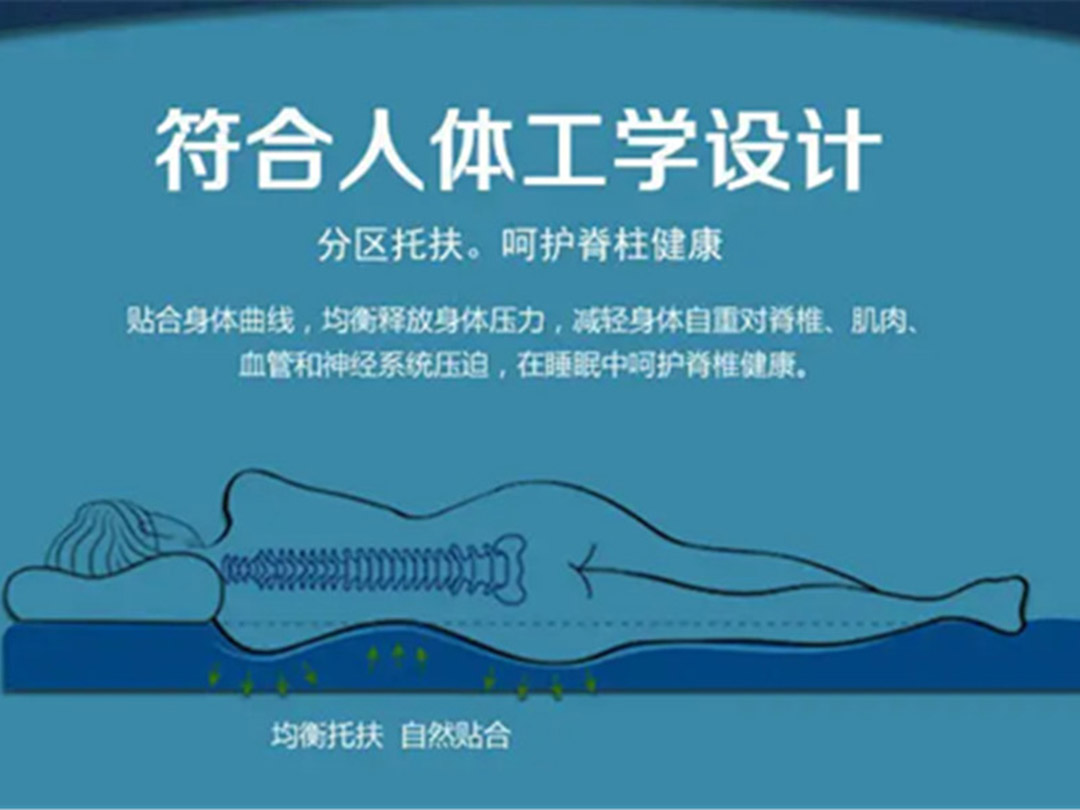
Data collection
Use the WeChat app to search for nearby branded stores and experience shops where data can be collected, and go to collect your personal sleep pressure distribution data.
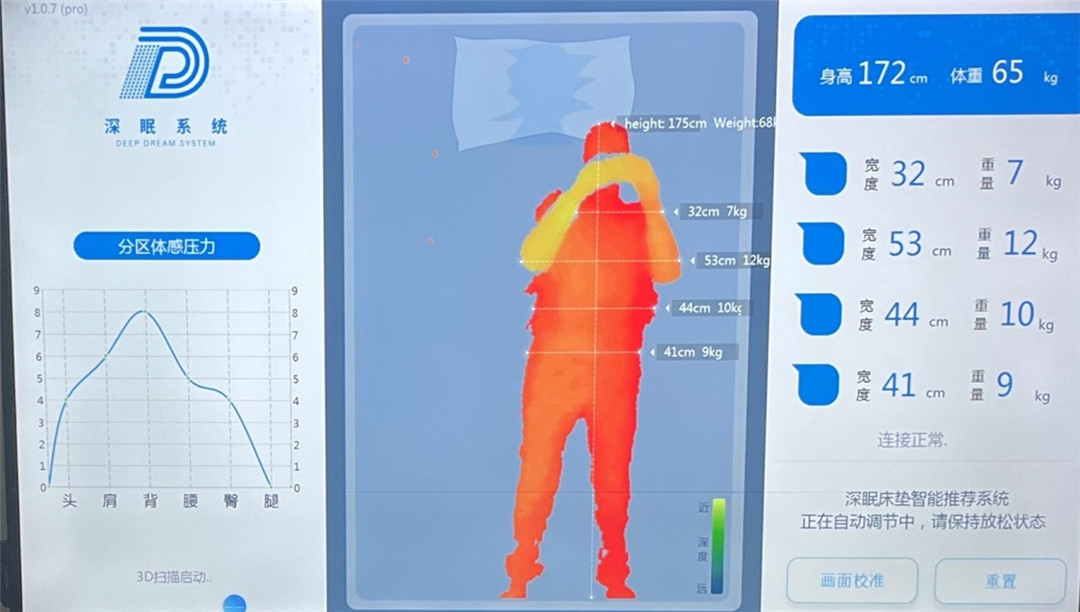
Mobile Ordering
Users place their own orders by mobile phone, ensure the integrity of the data collected, fill in the relevant personalisation and delivery information, place the order and make payment.
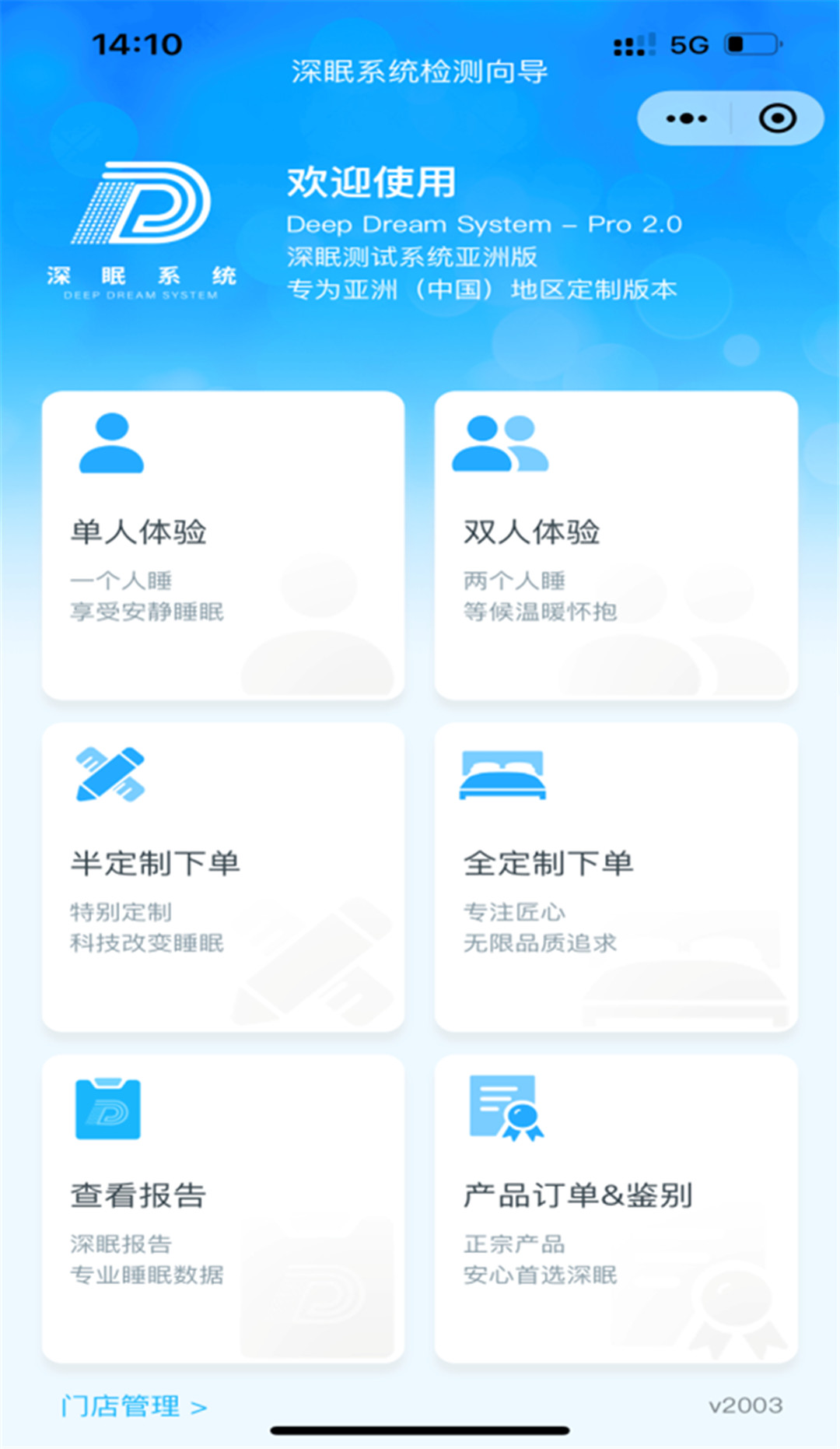
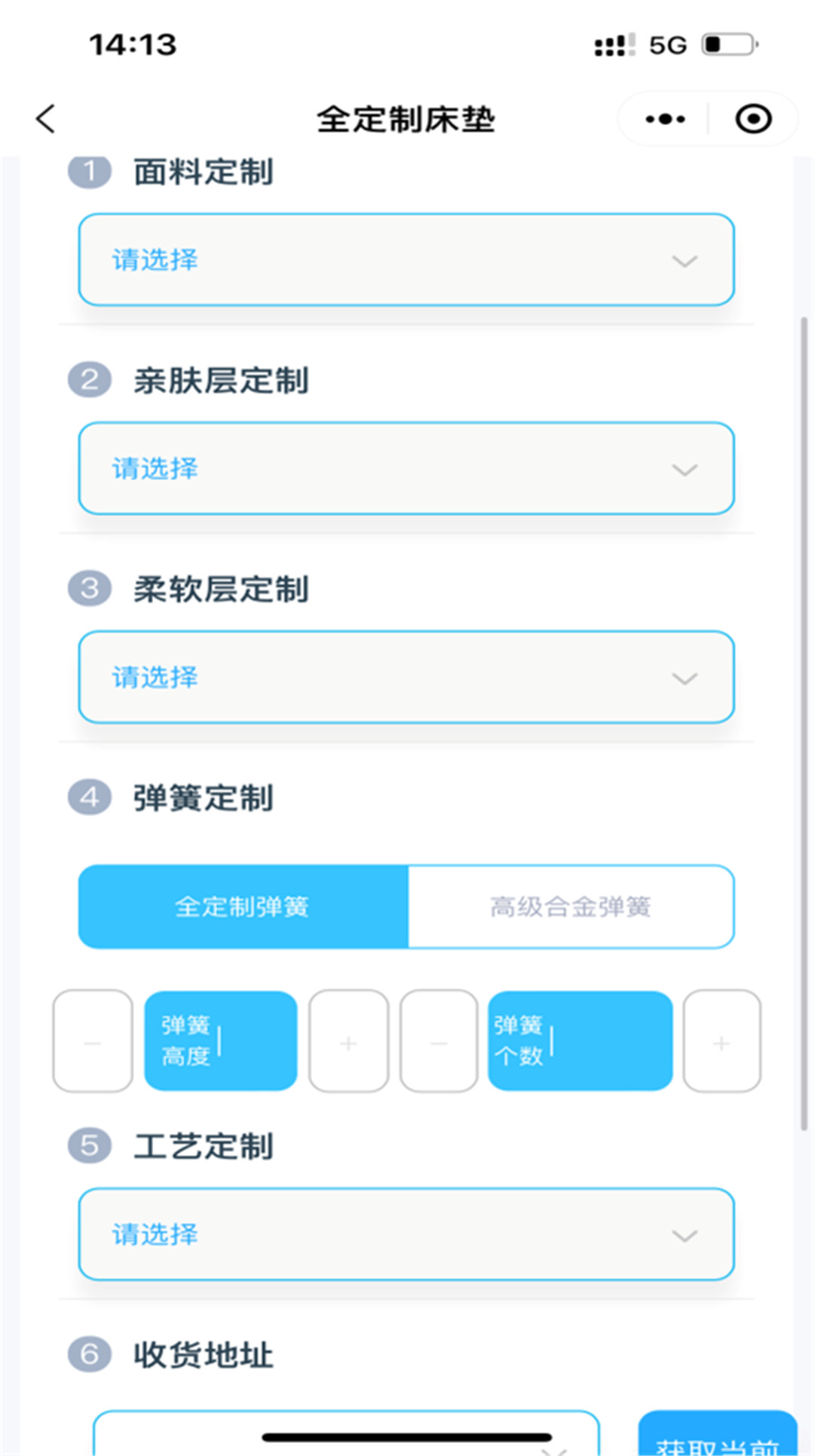
Factory takes orders and produces
The factory receives the user's order, forms the order information and, according to the relevant parameters of the user's order, arranges the appropriate equipment to produce the mattress. According to the parameters of the order, the equipment adjusts the steel wire specifications, the height of the spring package, etc. to control the support strength of each area, and produces a mattress that meets the pressure parameters of the user's sleeping posture. The mattress is then compressed and packaged by special compression and packaging equipment.
Logistic delivery
The finished packaged mattress is delivered by logistics to the user's address. The size of the mattress is significantly reduced by compression packaging, allowing easy access to lifts, through room doors, etc.
Use by the user
After receiving the mattress, the user can easily unpack it, the compressed mattress will rebound and a personalised mattress is ready for use. After use, the user can evaluate the mattress in the order screen or request customer service.
Personalisation options 1:
Soft and firm zoned mattresses such as 5 and 7 zones can be produced. Based on the collected height and weight data, the appropriate soft and firm zone parameters (wire size, mattress thickness, soft and firm position, etc.) are generated and the corresponding mattress is then automatically produced by the equipment.
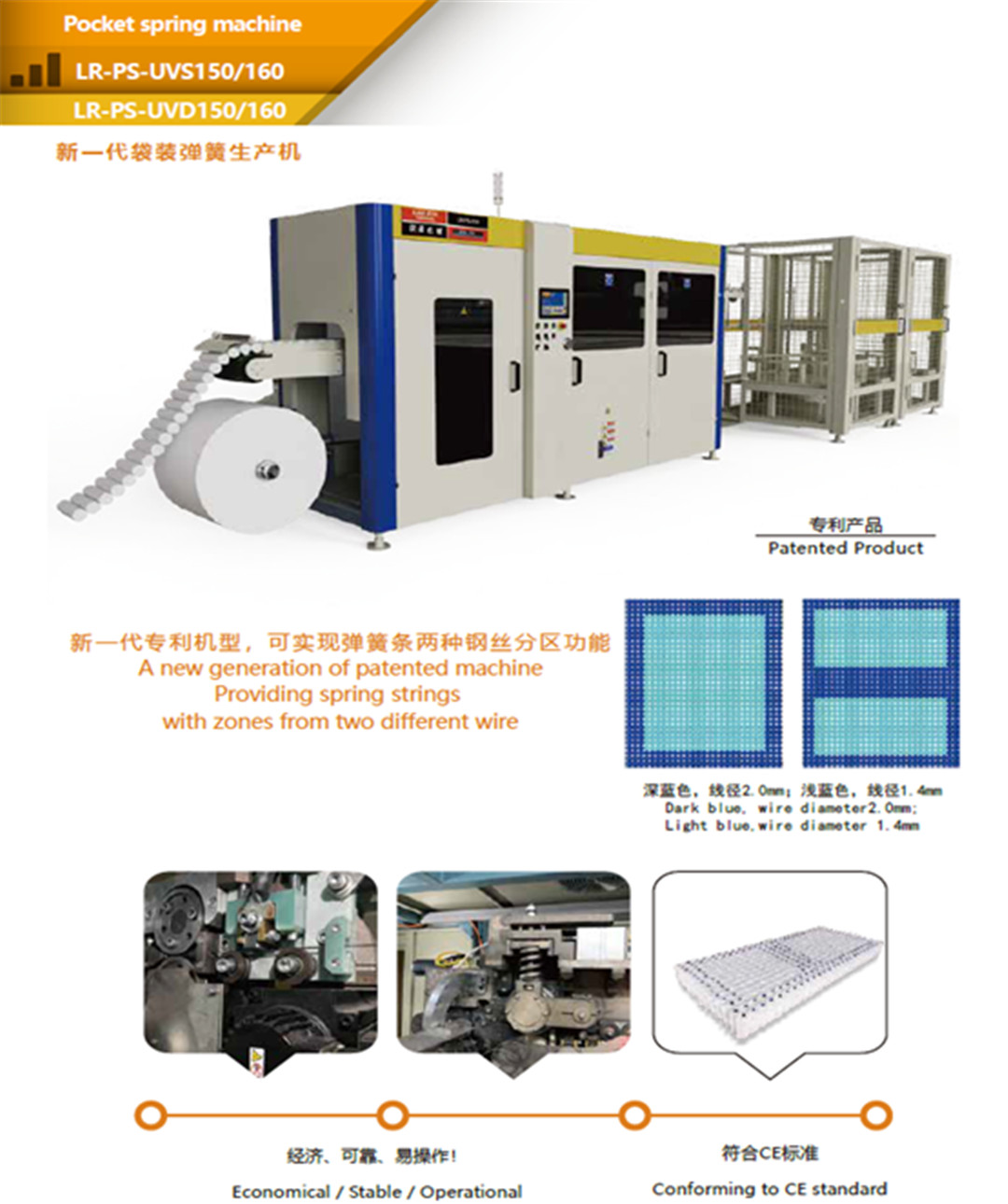
The double wire coiling technology enables the automatic production of zoned pocket spring mattresses by freely switching between wire sizes and adjusting the softness of different areas of the pocket spring strings according to preset parameters while the pocket spring machine is working. The maximum production speed is up to 200 springs/min.
Personalisation options 2:
Based on the collected height, weight and sleep pressure data, the corresponding spring support data is generated and the production equipment produces double pocket springs according to the data parameters, which can automatically adjust the height of the upper and lower spring layers to form a double pocket spring string with graduated support, which is then glued by a gluing machine into a double pocket spring bed core according to the predetermined length and width of the mattress. This solution offers a higher degree of personalisation and a better and more pronounced user experience. It can be used for both single and double mattresses.
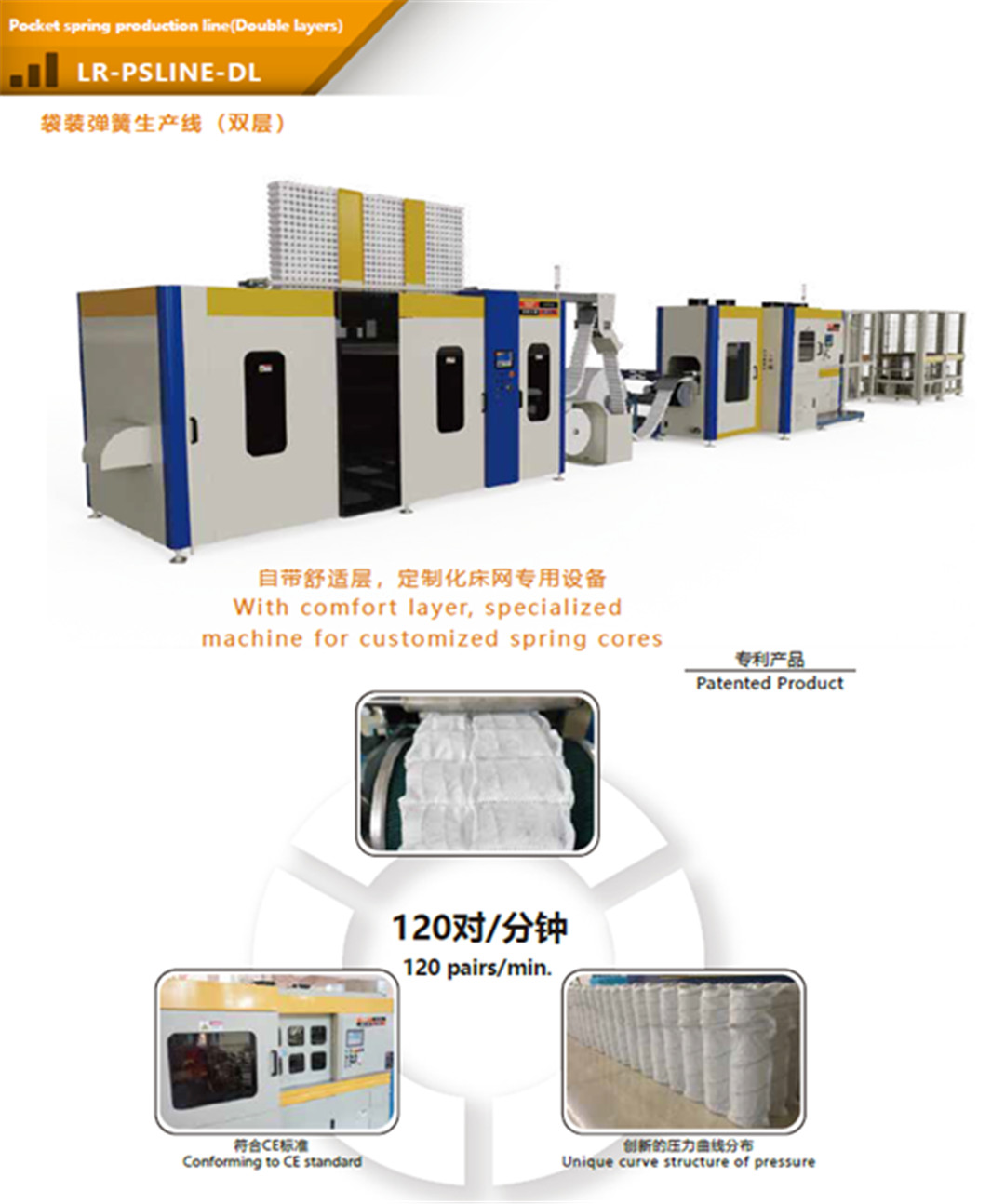
The core patent for the double layer pocket spring production technology has been awarded the Chinese Patent Award. The change in support is achieved by adjusting the compression height of the pocket spring, and as the upper comfort layer changes, the lower support layer adjusts its height accordingly, keeping the height of the entire mattress consistent. The upper and lower layers are welded together in one piece, eliminating the need for glue bonding, resulting in higher production efficiency and a more environmentally friendly product. Maximum production speed 120 pairs of springs/min.
Post time: Apr-21-2023